An essential guide on predictive maintenance
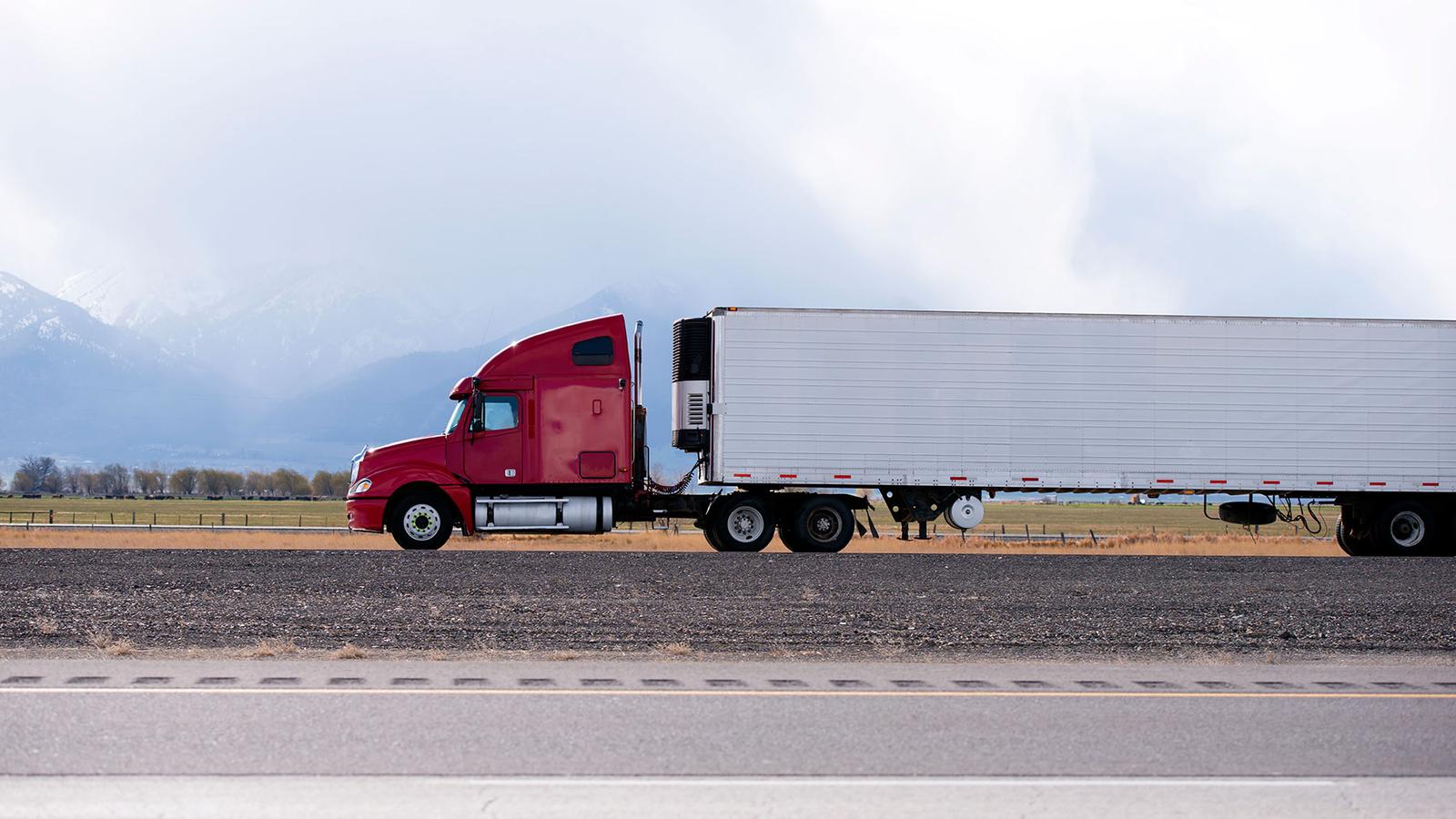
Predictive maintenance is a technique that uses data to detect issues with devices before they experience downtime. Find out more here.
Imagine we lived in a world where you knew all of the inconveniences you might face in a day or week before they happened. An employee calling in sick? A pothole in the road leading to a popped tire? If you knew things like this would happen, you’d know how to fix or avoid them. You could schedule another employee to cover a shift ahead of time instead of scrambling at the last minute. You could take another road or drive slowly over the pothole to avoid major damage.
While we can’t see the future, there is a technology that can predict and mitigate certain challenges. It’s called predictive maintenance. Let’s take a look at how it works.
Use the links below to jump to what you need:
- What is predictive maintenance?
- The importance of predictive maintenance
- How does predictive maintenance work?
- Type of predictive maintenance
- Benefits of predictive maintenance
- Steps for implementing predictive maintenance
- Real-life example of predictive maintenance
- Predictive maintenance needs and avoid disruptions with Hologram (#Predict maintenance needs and avoid disruptions with Hologram)
What is predictive maintenance?
Predictive maintenance might not be advanced enough yet to read the minds of your employees to tell you when they’ll call out sick, but it can give you an accurate estimate of when your machinery and other assets will break and need repair.
Using monitors, sensors, historical data, and algorithms, predictive maintenance systems determine when an asset or machinery will fail so owners and operators can plan accordingly and minimize repair costs. Let’s look at a very simple example: your cell phone.
Let’s say you’ve tracked data around your cell phone usage for the past three years. You monitor how many hours you use it and when you run into problems and find that every 300 hours of use, the phone breaks. With that in mind, you’d know to schedule maintenance every 295 hours so that the phone doesn’t break right when you need it. You may even be able to book time with your repair person early and get a discount on the cost of work.
While this is a fictional (and overly simplified example), it illustrates the power of predictive maintenance. Essentially, the system collects and analyzes data to determine the best time to repair and work on an asset to save time, money, and resources.
The importance of predictive maintenance
If there’s one guarantee when it comes to physical assets and machinery, it’s that they will need maintenance and proper care to extend their usefulness and longevity. Knowing this, it only makes sense to be strategic about these repairs so that they’re done most efficiently and cost-effectively while minimizing cascading impacts.
While predictive maintenance can be beneficial for any organization with capital tied up in machinery and similar assets, fleet owners may find it particularly beneficial. Predictive maintenance can be implemented to monitor truck and fleet performance to catch any issues just before they happen. This will save fleet owners money, as most repairs can be planned for, and keep drivers safe when they’re on the road.
How does predictive maintenance work?
A successful predictive maintenance system requires three things: condition-monitoring sensors, IoT technology, and predictive data models. The system starts with the sensors, which can be placed in machinery to monitor different factors and variables. For example, these sensors may monitor and collect data about temperature, vibrations, pressure, noise, or other elements depending on the machine.
Then, using the internet of technology, these sensors communicate with each other and a central control system to collect and send data in real-time. This data is then fed into predictive data models and algorithms, which are based on both real-time and historical data, to determine when the machine may fail.
While these algorithms can be extremely complex, they essentially compare a machine’s actual performance with its expected performance to determine how likely a machine is to fail. Deviations from expected behavior indicate deterioration that could lead to failure.
Recommended reading: The future is here: AI meets IoT
Types of predictive maintenance
Depending on the machine and your organization’s needs, the type of predictive maintenance you use may differ. Let’s look at some common examples to see how these varieties differ.
Vibration analysis
When it comes to machinery, vibration analysis can help identify root problems and determine if a machine will fail in the near future. Vibration analysis makes use of sensors to monitor the vibration of rotating parts to predict if a machine may need maintenance soon. The sensors measure frequency, velocity, displacement, and acceleration along all three axes of movement.
Acoustic analysis
While vibration analysis monitors for vibration anomalies, acoustic analysis does this for sound. By implementing sensors that keep track of and analyze sounds, owners and operators can be alerted to potential issues before they result in machine failure. For example, in a truck, acoustic analysis may detect brake problems that can be mitigated before they lead to a bigger — and potentially dangerous — problem.
Infrared analysis
Another way to apply predictive maintenance is through the use of infrared analysis. This technology monitors heat to track operating conditions and performance. Through infrared analysis, sensors may pick up that electronic equipment is overheating, that there is faulty insulation, or issues in the electrical switchgear, for example.
Recommended reading: What is IoT Analytics?
Benefits of predictive maintenance
Predictive maintenance can be a heavy lift upfront, as it takes money and resources to get an effective system up and running. However, it can be well worth the effort. Let’s look at a few benefits of predictive maintenance:
Saves your organization money
One of the biggest benefits of predictive maintenance is that implementing this type of system can save you money in the long term. For example, consider preventative maintenance, a type of maintenance you may be familiar with. Here, you’d routinely service machinery regardless of how it’s performing with the goal that it always stays in top shape. While this could be effective, you may end up spending more money in the long run to fix problems that aren’t even there. With predictive maintenance, you only repair assets when they are going to break, saving money and other resources.
Predictive maintenance maximizes efficiency
Predictive maintenance means that repairs happen in the most efficient way possible. By continuously monitoring the performance of a machine or asset, it minimizes the need for people to do this job. This also means there is no wasted time servicing equipment or giving it a “check-up” when nothing is actually wrong. Additionally, you’ll have an accurate idea of when equipment will fail so you can plan accordingly.
Equipment downtime is decreased
Knowing that at some point or another, most machines and equipment will need repairs, it only makes sense to try to do those repairs with the least disruption and downtime possible. Predictive maintenance makes this possible. For starters, when repairs need to happen, you will already know what needs fixing and what supplies you’ll need to do that. For example, let’s say you’ve used predictive maintenance and learn that one of your trucks will need new brakes within the next month. You can organize the repair around delivery schedules, part and labor availability, and ensure the repairs happen quickly and efficiently to minimize equipment downtime.
Improved safety and quality conditions for everyone
A lot of heavy machinery that could benefit from predictive maintenance is also operated or used by people. When this equipment is not working properly, it can be dangerous for those who interact with that machinery every day. Predictive maintenance lets you know exactly when there is a problem that needs addressing, keeping your employees and the people around them safer.
Steps for implementing predictive maintenance
If predictive maintenance sounds intriguing, you may be wondering how to actually implement and set up a system like this. While the steps may vary depending on objectives, industry, and equipment type, below is a high-level overview of how something like this works.
1. Establish acceptable conditions for sensors
As mentioned previously, predictive maintenance works by analyzing optimal performance against actual performance. To do this, you first have to establish what “optimal” actually means. Generally, this includes looking at historical data and other factors to determine the acceptable conditions you expect the sensors to report. When deviations to these standards occur, this is when you know maintenance may be required. As you get more data from the sensors, the acceptable conditions may change to reflect real-time data, which ultimately improves prediction accuracy.
2. Attach IoT devices
After determining the acceptable conditions for sensors, attach the desired IoT devices to the machines. Depending on your objectives and equipment, this could be vibration, acoustic, infrared, oil, or pressure sensors.
3. Connect IoT device to CMMS or remote dashboard
After connecting the IoT devices to the machines, the next step is to connect the devices to a computerized maintenance management system (CMMS) or remote dashboard. This is how the data the sensors collect will be analyzed and stored to make maintenance predictions.
4. Plan and schedule maintenance
As the system starts running, you should be alerted when maintenance is necessary. When the time comes, you’ll be able to plan and schedule your maintenance accordingly.
Real-life examples of predictive maintenance
Predictive maintenance isn’t just a far-out idea for a better future; it’s happening every day across various industries. Let’s take a look at a few real-life examples of predictive maintenance in action.
Refrigeration sensors: temperature sensors
Phase IV Enginering Inc., a sensor manufacturing company, makes wireless sensors for refrigerators that monitor temperature, current, vibration, and more to predict equipment failure. Commercial refrigeration can have a lot of moving parts, and failure could have potentially dangerous or costly effects. Imagine a refrigerator fails with medicine inside that makes the entire batch unusable. The same thing could happen with food. While the product itself would then be dangerous for human use, it could also be extremely costly to the owners to lose that much product. With predictive maintenance, you may be aware of a freezer’s declining performance and can move all of the products to a different refrigerator, fix the broken one, and avoid a costly, unplanned situation.
Oil and gas industry: oil management
According to Birlasoft, the oil and gas industry averages 27 days of unplanned downtime each year, costing a total of $38 million. The oil and gas industry uses older machinery, making it even more necessary to stay on top of any issues or necessary repairs. One oil and gas company implemented predictive maintenance on one of its nine offshore oil platforms before rolling the system to all other platforms. Through this, the company reduced downtime by an average of 20%, increasing production by an average of 500,000 barrels of oil annually.
Automotive industry: fleet management
In the automotive industry, a broken car or truck can make it difficult, if not impossible, to carry out basic job functions, not to mention impact the supply chain, cost money to repair, and cause potential dangers for drivers as well as everyone else on the road. Predictive maintenance in fleet management can help mitigate all of these issues. Sensors can be embedded into the vehicles to monitor various elements and accurately predict when a truck needs servicing. When this happens, owners can plan accordingly to ensure everyday business needs are still met and all operable vehicles function in the way they’re meant to.
Predict maintenance needs and avoid disruptions with Hologram
Predictive maintenance requires three things: sensors, IoT technology, and predictive models. Hologram’s global IoT SIM card can connect your sensors to the internet, making it easier than ever to monitor, analyze, and better manage your machinery and equipment. With coverage available in 200 countries and 470+ carriers to rely on, Hologram SIM cards automatically switch to the best available network. Connect across every technology from 2G to 4G LTE and new CAT-M. With Hologram, it’s easier than ever to employ predictive maintenance. Get connected today.