E-BOOK
The rise of robotics and cellular IoT in distribution and manufacturing
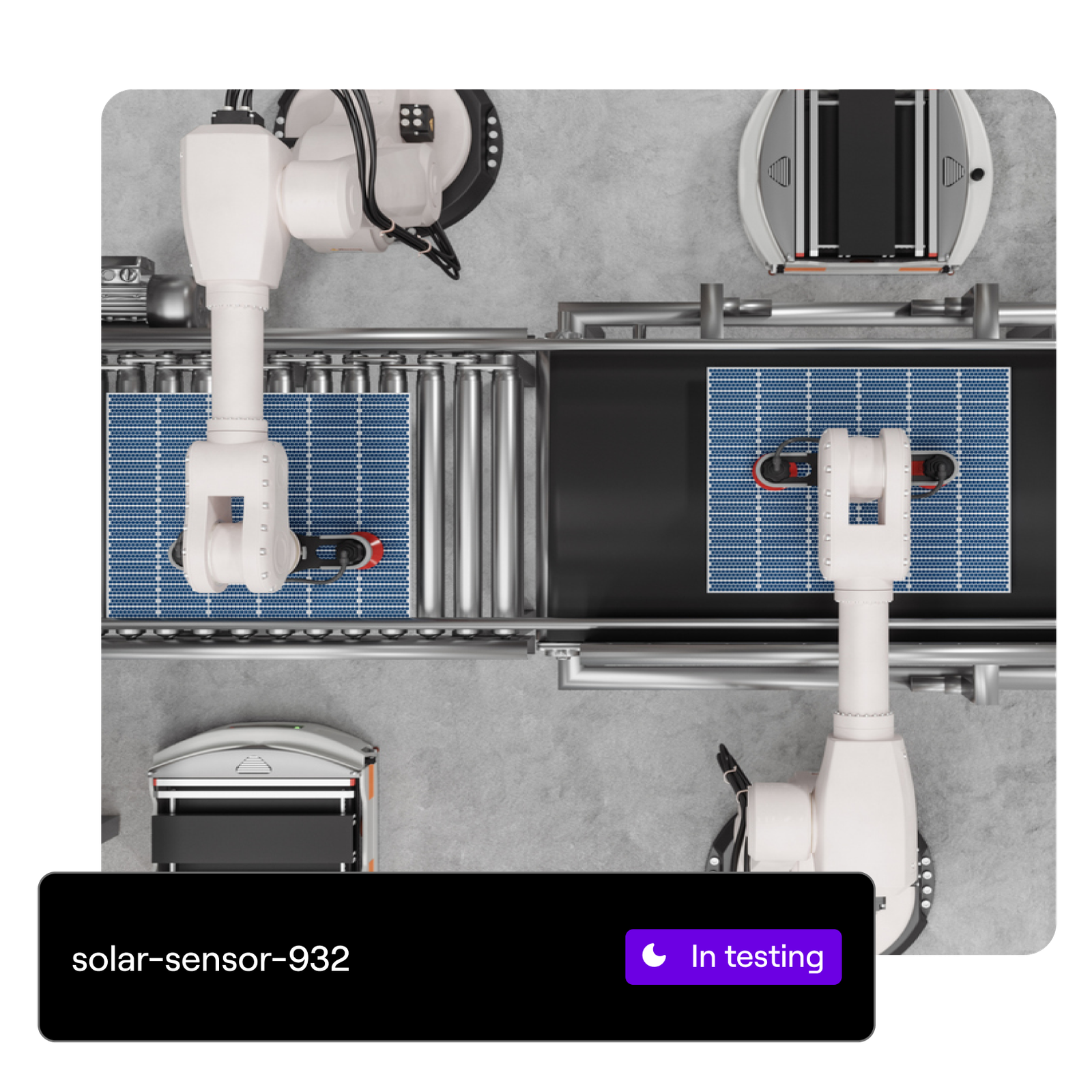
Robotics and automation are reshaping the manufacturing landscape at an unprecedented pace. The International Federation of Robotics reports nearly 4 million single-function robots already operating in industrial settings today. According to Gartner's predictions, by 2028, a staggering 75% of large enterprises in product-centric businesses will have integrated intralogistics smart robots (ISRs) into their warehouse operations.
Robotics deliver value across manufacturing sectors
On manufacturing floors, these advanced machines are taking on increasingly complex tasks, ranging from material transport to direct collaboration with human workers. These smart robots can autonomously navigate factory spaces, avoiding obstacles and adapting to dynamic environments. They're capable of performing intricate assembly operations, quality control inspections, and even collaborating with human workers on complex tasks.
- In automotive manufacturing, ISRs equipped with computer vision can detect minute defects in paintwork or panel alignment that might escape human notice.
- In electronics assembly, they can handle delicate components with precision, reducing errors and improving overall product quality.
- 3D printing robots are revolutionizing prototyping and small-batch production, creating complex parts on demand.
- Welding robots, guided by AI and machine vision, perform precise joins in metalworking with consistency that surpasses human capabilities.
Take Amazon's fulfillment centers, for example. They deploy an army of AI-powered robotic arms working "in all key production areas" of their three-million-square-foot facilities. These robots use machine learning to adapt to ever-changing inventory layouts and order patterns. They can identify, grasp, and move a wide variety of items with precision, even adjusting their grip strength based on an item's fragility. This intelligent automation has dramatically increased Amazon's order processing speed and accuracy.
Improving quality and reducing defects
Robots equipped with sensors can provide quality control and defect detection across industries. According to a recent study by the International Federation of Robotics, manufacturers implementing robotic quality control systems have reported up to a 90% reduction in defect rates, leading to significant cost savings and improved product reliability.
- In the food and beverage industry, robots equipped with advanced sensors perform quality control checks, detecting contaminants or packaging defects at high speeds.
- In the pharmaceutical industry, robots equipped with advanced sensors conduct rigorous quality control checks, identifying impurities or inconsistencies in drug formulations.
- Similarly, in electronics manufacturing, robotic systems use high-precision sensors to detect microscopic defects in circuit boards and components.
- The automotive sector employs sensor-laden robots to inspect paint quality, panel alignment, and safety-critical parts.
- In the textile industry, automated systems with specialized sensors examine fabric for flaws or color inconsistencies. Even in agriculture, robots with multispectral sensors.
The integration of ISRs is not just enhancing efficiency; it's fundamentally changing how production lines are designed and operated. As more companies adopt similar technologies, we're seeing a radical transformation in factory and warehouse operations, with robots becoming essential collaborators alongside human workers.
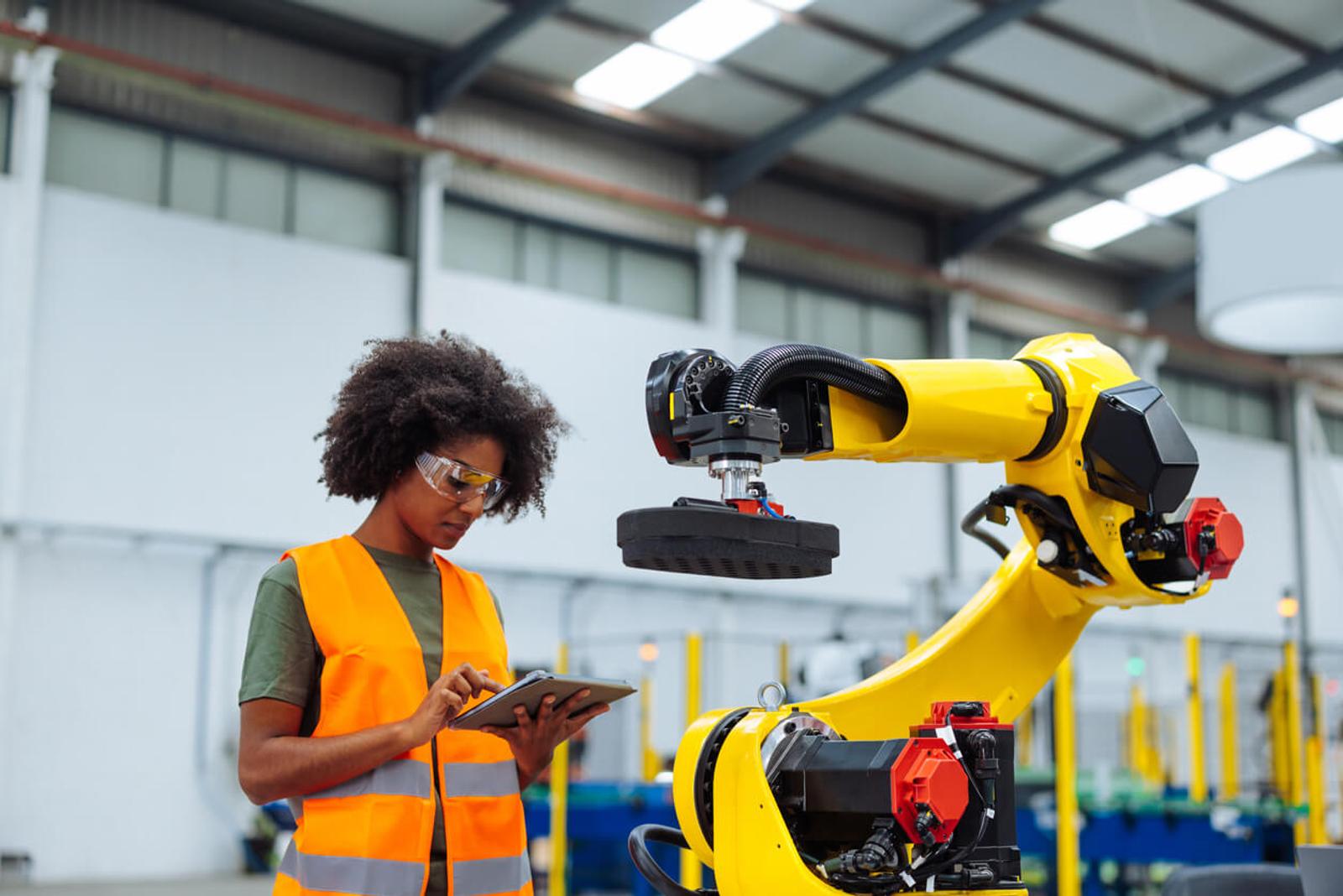
Delivering worker safety
The advantages of robotics extend far beyond these efficiency gains, particularly with worker safety. Manufacturers are deploying IoT-enabled collaborative robots (cobots) and automated guided vehicles (AGVs) to create safer work environments.
- For instance, cobots equipped with force sensors can handle hazardous chemicals in pharmaceutical plants, minimizing human exposure to toxic substances.
- In automotive manufacturing, AGVs transport heavy engine components across factory floors, reducing the risk of musculoskeletal injuries associated with manual lifting.
- In warehouses, cobots assist with high-reach tasks, eliminating the need for workers to climb ladders or operate potentially dangerous forklifts at height.
These applications not only protect workers from immediate physical harm but also contribute to long-term occupational health improvements.
Cellular connectivity is essential
Gartner forecasts a future where smart robots outnumber human frontline workers in many industries by 2028. Cellular IoT connectivity serves as the backbone for that robotic revolution. It delivers the essential infrastructure for seamless communication and coordination of large fleets of mobile robots and automated guided vehicles (AGVs) across expansive factory floors and warehouses. As the manufacturing sector becomes increasingly automated, implementing a robust cellular IoT strategy is even more critical.
The low-latency, high-reliability connectivity offered by cellular networks enables robots to respond to changing conditions in near real-time. Plus, the advent of 5G networks enables more sophisticated and data-intensive applications for industrial robotics.
Gartner's research indicates that by 2026, half of all edge computing deployments will incorporate machine learning, a significant jump from just 5% in 2022. This surge in edge AI capabilities powered by cellular IoT empowers robots to make split-second decisions and adapt swiftly to new situations, further enhancing their effectiveness in industrial settings.
“We're seeing a significant increase in the market for cellular IoT to ensure the reliability that's needed to put that edge data into use."
– Pat Wilbur, CTO, Hologram
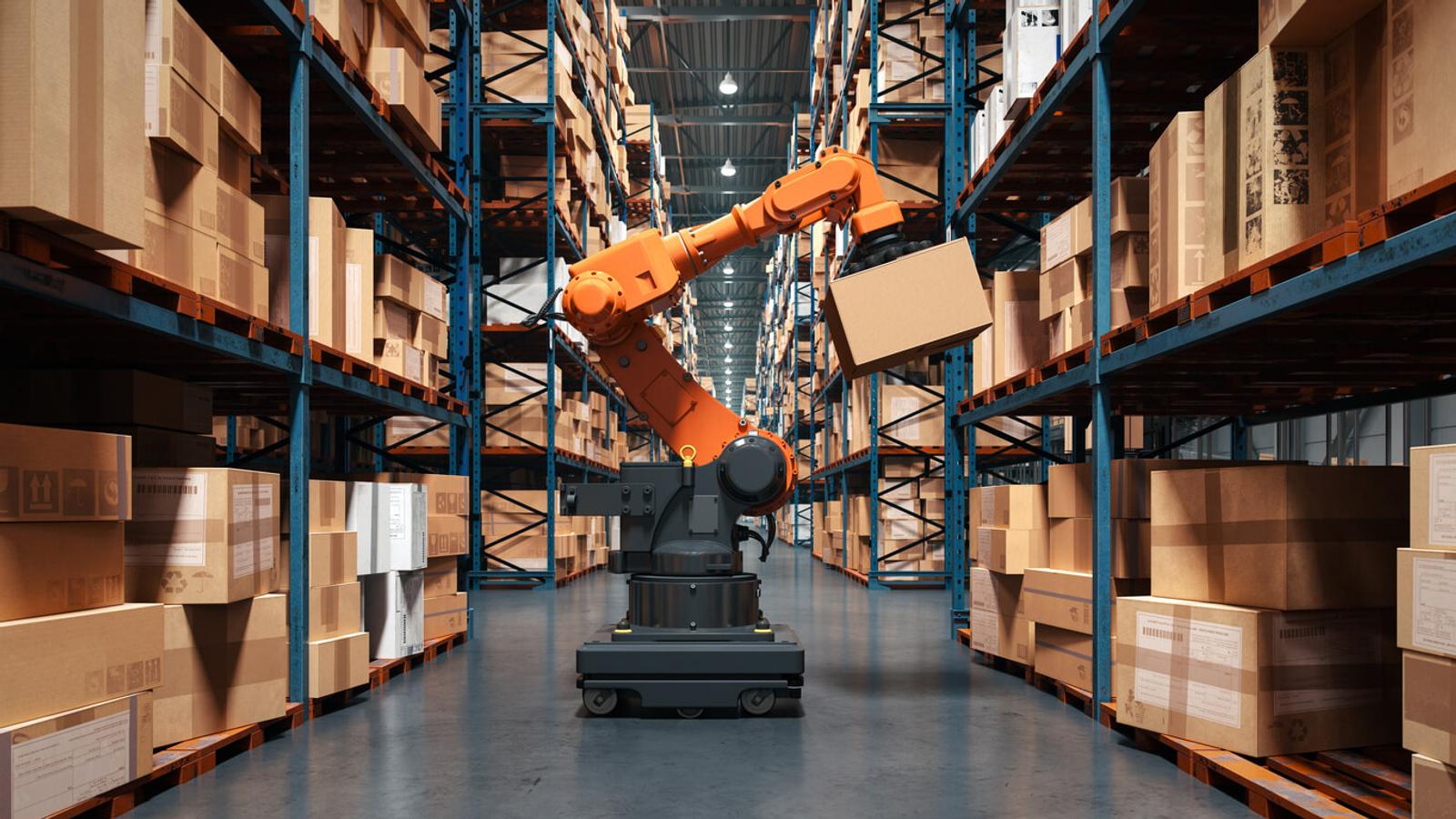
Turning data into intelligence
Cellular IoT enables manufacturers to collect and analyze enormous volumes of operational data from machines and sensors in real-time. This data-driven approach allows for continuous optimization of manufacturing processes, leading to improvements in efficiency, quality, and cost-effectiveness. By leveraging advanced analytics and machine learning algorithms, manufacturers can identify bottlenecks, predict maintenance needs, and fine-tune robotic operations for peak performance.
According to a recent study, manufacturers implementing predictive maintenance strategies have seen a 20% reduction in maintenance costs and a 50% decrease in unexpected downtime. The same data used for optimization can help with remote monitoring and predictive maintenance capabilities to ensure that the robots remain operational and reliable. By analyzing sensor data from robots and other equipment, manufacturers can detect subtle changes in performance that may indicate impending failures. This allows maintenance teams to address issues before they cause costly downtime.
Machine learning algorithms can analyze historical data from cellular-connected robots to predict potential failures before they occur, allowing maintenance teams to schedule repairs proactively and minimize disruptions to production schedules. Remote monitoring allows technicians to diagnose issues without physically being on-site, enabling faster response times and reducing the need for in-person inspections.
Digital twins for optimization
Cellular-connected robots generate vast amounts of data that manufacturers can harness to create digital twins of their production processes. These virtual replicas enable engineers to simulate and test modifications to assembly lines without interrupting ongoing operations. By experimenting with different scenarios in the digital realm, companies can fine-tune robot movements, optimize assembly sequences, and reconfigure factory layouts for peak performance.
According to a recent Gartner survey, 13% of organizations implementing IoT projects already use digital twins, while 62% are either in the process of establishing digital twin use or plan to do so within a year. Digital twins are gaining traction across diverse industries.
- In manufacturing, Siemens uses digital twins to model entire factories, allowing them to optimize production flows and predict maintenance needs. This approach has led to a 30% reduction in machine downtime and a 20% increase in overall equipment effectiveness.
- The aerospace sector also benefits from this technology, with Boeing and Airbus employing digital twins to simulate aircraft performance and maintenance requirements, thereby minimizing downtime and enhancing safety.
- Automotive manufacturers leverage digital twins for vehicle design and testing, accelerating development cycles and streamlining production processes.
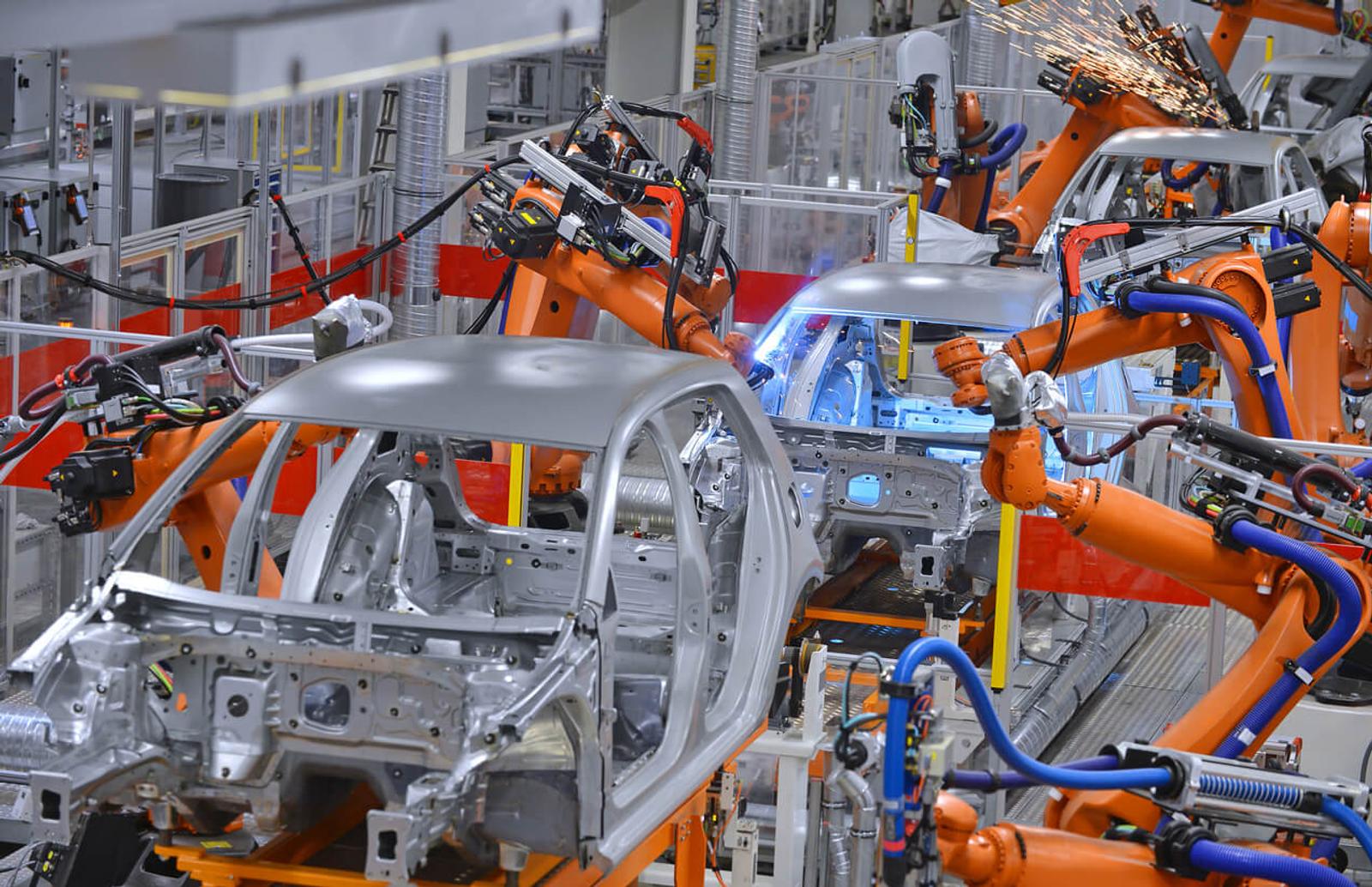
Challenges with connected manufacturing
While the potential of robotics is immense, it's important to acknowledge the challenges - both technological and human - that manufacturers face in adopting these technologies.
- Manufacturers need to invest in robust cybersecurity measures to protect their connected robotic systems.
- Security needs to be considered from the start and as part of a comprehensive strategy, as connected robots could potentially become targets for cyberattacks. Integrating new robotic systems with legacy manufacturing equipment and software can also be complex and costly.
- Additionally, the workforce implications of increased automation must be carefully managed, with a focus on retraining and upskilling employees for new roles alongside robotic systems.
- Companies must focus on change management and workforce development to help employees adapt to and thrive in an increasingly automated environment.
Cellular IoT + robotics delivers a competitive advantage
Cellular IoT is becoming increasingly crucial for automation and robotics in manufacturing. Its ability to provide reliable, low-latency connectivity across large industrial spaces enables seamless coordination of complex robotic systems. These systems deliver significantly increased productivity, quality, and worker experiences in industrial environments.
Plus, the robots and sensors connected by cellular IoT deliver the real-time data needed for optimization, remote monitoring, digital twins, and more. According to a recent market report, the global cellular IoT market is expected to grow at a compound annual growth rate (CAGR) of 21.4% from 2023 to 2030, reaching a value of $61.0 billion by 2030. This rapid growth underscores the increasing recognition of cellular IoT's importance in driving industrial automation and robotics forward.